Textile machines
Each model and each category of Elettrotecnica B.C. branded footwear manufacturing machines has several features that characterize it in an unmistakable way: total reliability in the manufacturing processes, maximum precision even in details, high performance in every production phase.
The same criteria are also respected in our series of textile machines: conceived for weaving the desired upper, the different models meet the most varied needs of footwear and textile product manufacturers. Some of their characteristics are unique, such as the bidirectional shrink function or the shoes processing speed; these and many other technical configurations allow to increase production while maintaining also an excellent quality of work.
Find out what makes our textile machines reliable and efficient, browse the catalog!
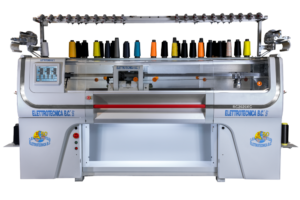
Contact us!
Go to the form to ask about our products!
Models
Electronic roller machine for yarns
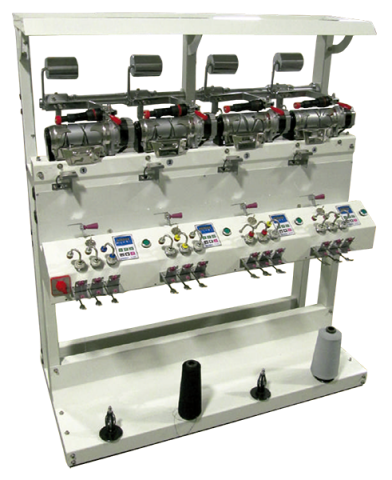
Technical details | |
---|---|
Dimensions: | cm 148 (58”) x 71 (26”) x 127 (50”) |
Net weight: | Kg 160 (LBS) |
Electric power: | Kw 0,8 |
Winding speed: | Max 1000 mt./min. |
Machine for the realization of the upper in 3D
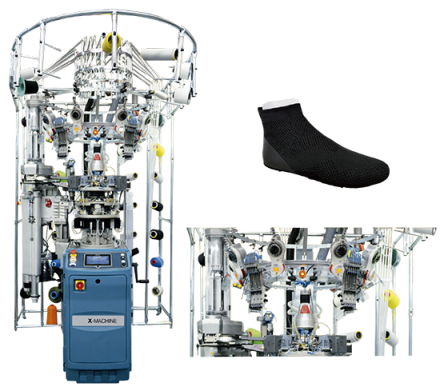
Single cylinder electronic knitting machine with 4 reciprocating-motion feeds and 2 points of selection per feed and rotation sense, which knits various technical Intarsia items. This system, patented, allows the possibility of patterning on all 4 feeds giving high definition and a sharpness of colour.
MAXIMUM SPEED:
180 rpm in unidirectional motion.
CYLINDER SELECTION:
Selection on the cylinder through actuators with 12 levels (8 in total: two for each feeder for both rotation senses).
SINKER CAP SELECTION:
Actuators with 6 levels (4 in total per sinker selection).
STRIPPING YARNFINGERS:
6 multi-position yarnfingers per feed.
TRAPPER FOR BARE AND COVERED ELASTIC YARN:
3 trappers per feed.
DIAL JACKS AND YARN CUTTER:
Yarn cutter saw release with up and down dial movement, driven by step motor to reposition the saw blade height.
SUCTION SYSTEM:
Take-down aspiration by 2 suction fans or a central suction system.
Items suction tube Ø 60 mm.
Items transfer tube Ø 60 mm.
Air limiting valve with electronic incremental programming
STITCH CAMS:
Stitch formation adjustment by step motors, independent on each feed.
Possibility of loop widening, tightening and shading on the same area and/or course.
Step motor to reposition cylinder height.
On board items sizing, adjustable in both cm. and inches.
MAIN KNITTING POSSIBILITIES:
Single or double welt carried out by dial jacks, in several selections, with knitted and laid-in elastic yarn. With 4 feeds on the same course: patterns and/or supports placed with Intarsia technology, eliminating cut yarns inside the item. Every knitted pattern has up to 3 technical ways. 4 feed selectable terry in both rotational senses.
SINKER CAP:
Closed-tracks cam box with angle cams position driven by a step motor for precise loop/stitch control
YARN FEEDERS:
6 mechanical yarn recoveries per each feeder (24 in total).
OPTIONAL:
Elastic feeders with step motor.
EFS920 Memminger – IRO for yarn recovery.
YARN SENSORS:
Latest generation of optical yarn sensors.
CREEL:
With rear yarn rack.
LUBRICATION:
Pneumatic pump with oil recycling.
MACHINE MOVEMENT:
Torque Motor.
ELECTRONIC CONTROLLER:
Integrated ‘quad core’ from Dinema for the serial checking of all electronic systems. Latest generation of graphic display with a
colour touch screen.
PROGRAMMING:
Software S.I.S. Plus with totally graphical integrated programming.
Technical details | |
---|---|
Diameter: | 4" |
Needle No.: | 96 - 108 - 120 - 120 - 132 - 144 |
Needle Gouge (GG): | 18 - 18 - 18 - 24 - 24 - 24 - |
Machine Gouge (GG): | 8 - 9 - 10 - 10 - 11 - 12 |
: |
Machine for the flat knitting of the 2d/3d uppers
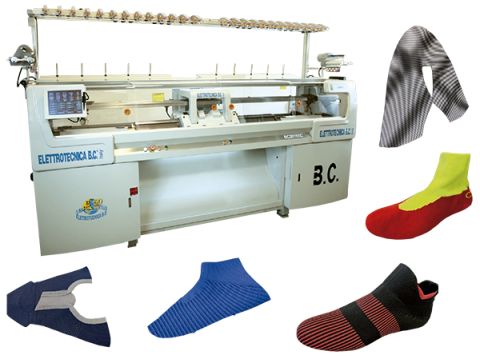
Machine for the flat knitting of the uppers, belonging to the second generation. The machine is in possession of unique functions in the field of flat knitting for footwear, among which: dynamoelectric cam, bidirectional narrowing function, forced overturning function, bilateral point function, needle adjustment function and multi-needle gauge and processing function of the left and right shoes. The maximum reachable speed of 1.7 m/s saves time increasing the production and processing of the upper. The machine is equipped with a dual-core CPU processor that allows to optimize and make flat knitting work easier, giving the possibility to customize the type of processing. System memory can be extended in an unlimited way and can save an infinity number of models. The excellent operating system installed, requires only a drawing layer to identify the inlays and knitting stitches needed for processing.
- DINAMOELECTRIC CAM: it can reach the needle for knitting and tuck tightly, with the possibility of adjusting the sealing intensity and the
processing of the upper in 3D; - BIDIRECTIONAL RESTRICTION FUNCTION: with regard to the difficult processing of some particular fabrics, this function allows to
considerably reduce the knitting line by working simultaneously on both sides and improving the efficiency of the machine to 90%. - FORCED OVERCURRENT FUNCTION: function that solves the global problem of closing the first needle in single or double jersey fabrics
- BILATERAL POINT FUNCTION: with the simple change of production values, the bilateral point can be adjusted to control the length of the upper.
- LEFT / RIGHT SHOES KNITTING CONTINUES: the fabric of the shoes can be knitted continuously with the possibility to set separately the amount of shoes left and right.
- FOUR WIRE POWER SUPPLIES: the machine allows the use of four wire feeders on each side during the knitting of waste cotton. Compared to the ordinary type, the line and quantity of waste cotton is reduced to 90%.
- INTELLIGENT PROGRAM: ability to display the positioning of the inlays and knit stitches with a single layer, without the need to add additional images or layers to the program.
- CROSSED SINKER: crossed sinker is suitable for 3D fabric molding in one pass
TECHNICAL DETAILS
- Needle: 12G, 14G, 7-14G multimeter.
- Knitting system: 2D / 3D.
- Knitting speed: Maximum speed 1.7 m / sec; 24-section programmable speed.
- Needle actuator: 8-position electronic actuator.
- Sinking system: Cross bar, stepper motor drive, can be adjusted according to the different , obtaining various shapes and patterns.
- Spot density: The control of the 32-section stepper motor controls measurement, the adjustable range is 0-650.
- Transfer system: Front and rear, which do not affect the direction of the cart.
- Take down device: High roller device that can make it easier and more precise.
- Electric motor rod: The electric motor drives the rod for greater accuracy.
- Adjustable fold: The density is adjustable.
- Forward spinning device: Roller wire feed device or wire storage ordering device to guarantee timely yarn delivery.
- Yarn feeder: 2 * 8 sets of wallets are located on the left and right side.
- Guide system: Belt drive, AC servo motor control.
- Data entry: Through the U disk, is possible connect the computer to enter the data.
- Protection: Automatic stop device in case of breakage of the yarn, knot of the yarn, dosing, percussion, completion, overload, designated start and end, program error, etc.
- Safety device: The machine is equipped with a carter to reduce noise and dust, the protective cover is equipped stop sensor , emergency stop, device shutdown and alarm indicator.
- Control system: The screen adopts an industrial LCD display with graphic touch control. The memory extension is 1G .
Technical details | |
---|---|
Dimensions: | cm 297(117") x 94(37") x 2010(791") |
Net weight: | Kg 1145 (2524LBS) |
Electric power: | Kw 2,0 |
Voltage: | 220 V |
Laser for upper cutting with projection system
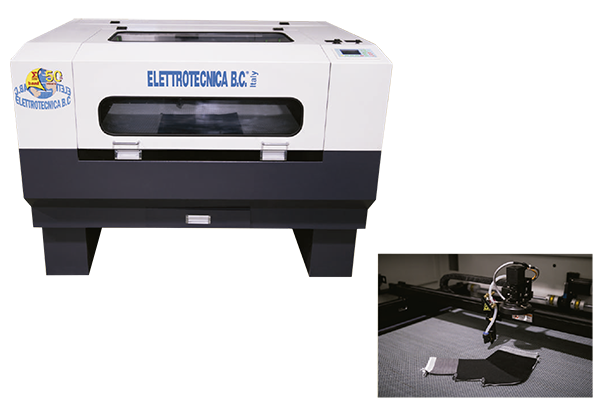
100W power laser equipped with a projector suitable for projection of working shapes, a system that guarantees perfect positioning of the upper on the work surface.
Work area dimensions cm. 60 x 90.
Technical details | |
---|---|
Dimensions: | cm 150 (59”) x 120 (47”) x 125 (47”) |
Net weight: | Kg 350 (772LBS) |
Electric power: | Kw 2,5 |
Capacity laser: | 100 W |
Cutting speed: | 0-36m / min |
Iron machine with vapor generator and aspiration table
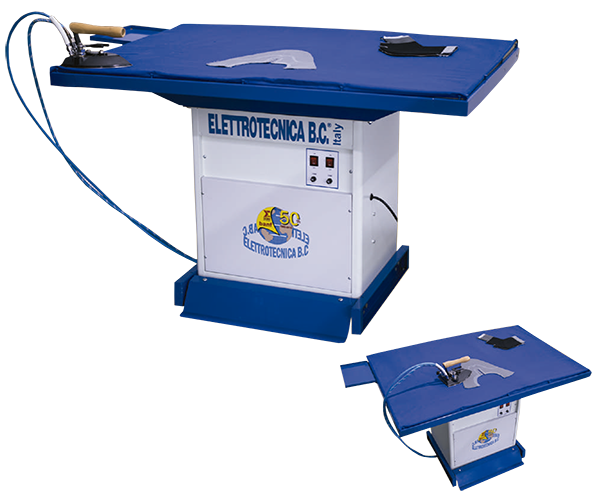
The ironing machine is equipped with a steam generator with an intelligent automatic control. It’s easy to use and recovers the steam in excess avoiding the waste of energy. It possesses an alarm of safe and intelligent water shortage and fast heating. It reaches the working pressure in 7 minutes and it can generate steam continuously. The perforated work surface is resistant and non-deformable ensures that the worktop remains always dry.
Technical details | |
---|---|
Dimensions: | cm 80 (32”) x 120 (47”) x 80 (32”) |
Net weight: | Kg 112 (247LBS) |
Electric power: | Kw 3 / 6 |
Aspiration power: | 750 W |
Empty pressure: | ≥ 150 PA |
Machine for the flat knitting of the 2D/3D uppers
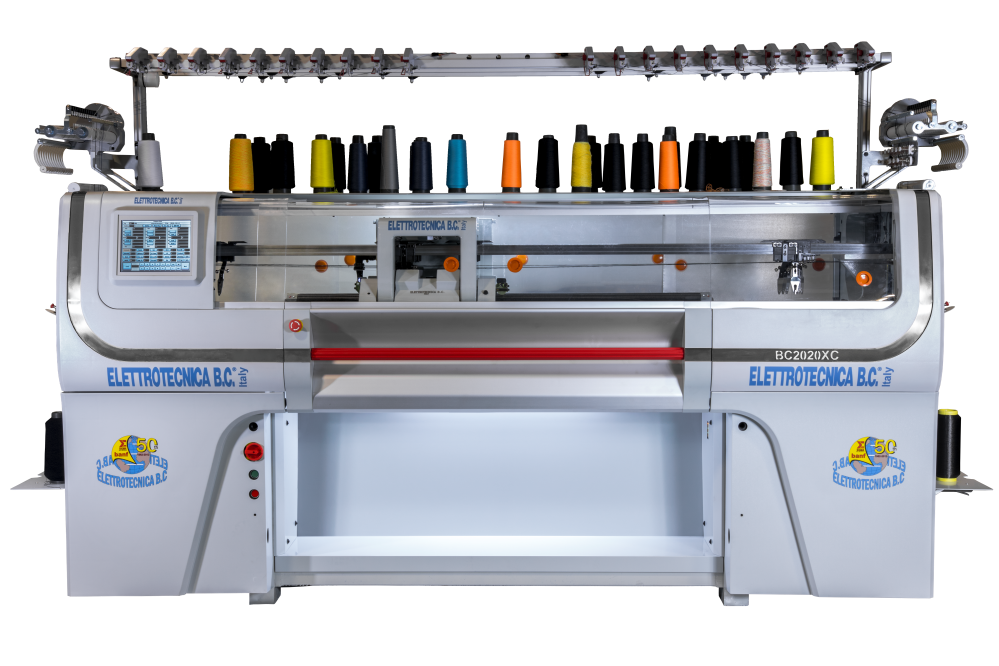
Machine for the flat knitting of the uppers, belonging to the second generation. The machine is in possession of unique functions in the field of flat knitting for footwear, among which: dynamoelectric cam, bidirectional narrowing function, forced overturning function, bilateral point function, needle adjustment function and multi-needle gauge and processing function of the left and right shoes. The maximum reachable speed of 1.7 m/s saves time increasing the production and processing of the upper. The machine is equipped with a dual-core CPU processor that allows to optimize and make flat knitting work easier, giving the possibility to customize the type of processing. System memory can be extended in an unlimited way and can save an infinity number of models. The excellent operating system installed, requires only a drawing layer to identify the inlays and knitting stitches needed for processing.
- DINAMOELECTRIC CAM: it can reach the needle for knitting and tuck tightly, with the possibility of adjusting the sealing intensity and the processing of the upper in 3D;
- BIDIRECTIONAL RESTRICTION FUNCTION: with regard to the difficult processing of some particular fabrics, this function allows to considerably reduce the knitting line by working simultaneously on both sides and improving the efficiency of the machine to 90%.
- FORCED OVERCURRENT FUNCTION: function that solves the global problem of closing the first needle in single or double jersey fabrics.
- BILATERAL POINT FUNCTION: with the simple change of production values, the bilateral point can be adjusted to control the length of the upper.
- LEFT / RIGHT SHOES KNITTING CONTINUES: the fabric of the shoes can be knitted continuously with the possibility to set separately the amount of shoes left and right.
- FOUR WIRE POWER SUPPLIES: the machine allows the use of four wire feeders on each side during the knitting of waste cotton. Compared to the ordinary type, the line and quantity of waste cotton is reduced to 90%.
- INTELLIGENT PROGRAM: ability to display the positioning of the inlays and knit stitches with a single layer, without the need to add additional images or layers to the program.
- CROSSED SINKER: crossed sinker is suitable for 3D fabric molding in one pass.
DATI TECNICI
- Ago: 12G, 14G, 7-14G multimetro.
- Sistema di lavoro a maglia: 2D/3D Velocità di lavoro: Velocità massima 1,7 m/sec;
- Velocità programmabile a 24 sezioni.
- Attuatore dell'ago: Attuatore elettronico a 8 posizioni.
- Sistema di affondamento: Traversino a croce, azionamento del motore passo-passo, può essere regolato in base al diverso tessuto, ottenendo varie forme e modelli.
- Densità del punto: Il controllo del motore passo-passo a 32 sezioni consente di regolare densità, l'intervallo regolabile è 0-650.
- Sistema di trasferimento: Anteriore e posteriore, che non influenzano la direzione del carrello.
- Dispositivo take down: Dispositivo High roller in grado di rendere il tessuto uniforme e liscio.
- Asta del motore elettrico: Il motore elettrico guida l'asta per una maggiore accuratezza.
- Piega regolabile: La densità è regolabile.
- Dispositivo di filatura in avanti: Dispositivo di avanzamento del filo del rullo o dispositivo ordinario di stoccaggio del filo per garantire la consegna del filato tempestivo.
- Alimentatore di filati: 2* 8 set di portafili sono distribuiti sul lato sinistro e destro.
- Sistema di guida: Trasmissione a cinghia, controllo servomotore AC.
- Inserimento dati: Attraverso il disco U è possibile collegare il computer per immettere i dati.
- Protezione: Dispositivo di arresto automatico in caso di rottura del filo, nodo del filato, dosaggio, percussione, completamento, sovraccarico, inizio e fine designati, errore di programma, ecc.
- Dispositivo di sicurezza: La macchina è dotata di un carter per ridurre il rumore e la polvere, la copertura protettiva è dotata di sensore di arresto, arresto di emergenza, spegnimento del dispositivo e indicatore di allarme.
- Sistema di controllo: Lo schermo adotta un display LCD industriale con controllo touch grafico. L'estensione della memoria è 1G
Technical details | |
---|---|
Dimensions: | cm. 310(122")x106(42")x201(79") |
Net weight: | Kg. 1145 (2524LBS) |
Electric power: | Kw 2,0 |
Voltage: | 220 V |
Belt ironing machine for 2d upper with knitting technology
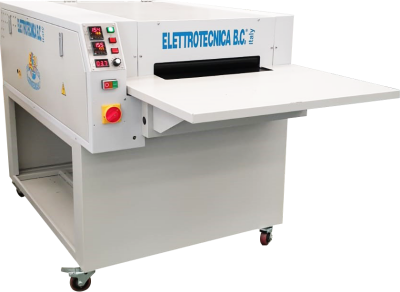
- Machine for ironing the uppers with an adjustable speed belt system;
- Separate upper and lower temperature regulation;
- Voltage regulation of the electric tape to obtain the maximum ironing quality for each type of thickness;
- Very high productivity up to 4000 pairs in 8 hours.
Technical details | |
---|---|
Dimensions: | Cm 262 (103”) x 97 (38”) x 107 (42”) |
Electric Power: | Kw 12 - AMP 24 - 400V |
Air consumption: | No |
Daily production: | 4000 pairs / 8 hours |
Cement reactivating machine Opanka/K
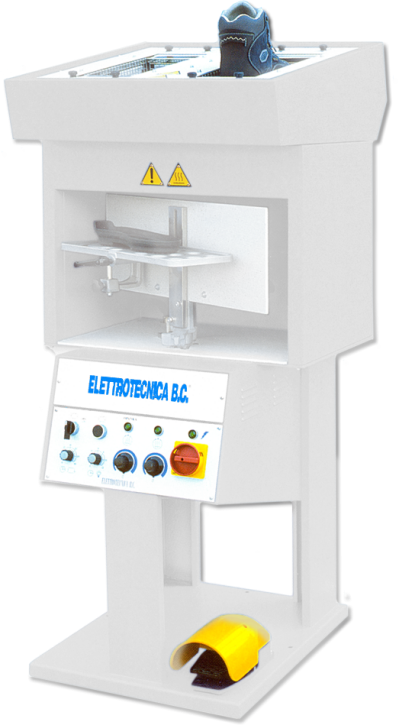
Cement reactivating machine, by means of an instantaneous infrared light source, enabllng rapid reheating of the cement-coated part of the sole and shoe. This system has the advantage of preventing excessive softening of the sole, particularly if in PVC.
Manual and automatic operation. Output according to sole press output.
Technical details | |
---|---|
Dimensions: | cm 77 (30”) x 64 (25”) x 139 (55”) |
Net weight: | Kg 102 (225 LBS) |
Absorbed Power: | Kw 6,4 |
Pneumatic assembling for soles complete at 1 station
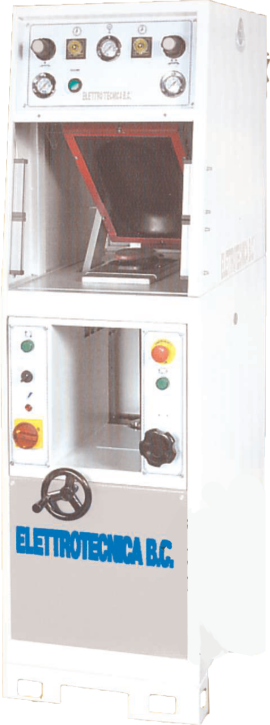
Pneumatic assembling machine for soles with blowing up bell
- Double inner chamber, one first pressure, one second pressure
- Adapted to whichever type shoe and boot
- Equipped of photoelectric cells for starting the automatic cycle and, for the emergency of the operator
- The shoe support is adjustable in vertical and horizontal
- New cycle of release that allows to speed the cycles
and to diminish the air consumption and the usury of rubbers - Montati di serie un accumulatore di aria e un impianto pneumatico con doppia portata di vuoto.
- It has a air storage cell and a pneumatic system with double capacity of vacuum. Adjustable times of first and second press individually until 30"
- Adjustable pressures first and second press individually
Technical details | |
---|---|
Dimensions: | cm 50 (20”) x 91 (36”) x 167 (66”) |
Net weight: | Kg 292 ( 644LBS) |
Electric power: | Kw 0,16 |
Air consumption at 7 Bar: | 27,5 lt/min |
: |
Sole assembly pneumatic at sink tube type
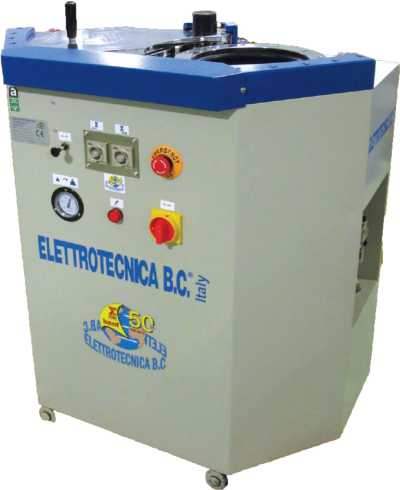
- Sole assembling pneumatic at sink tube type useful for all kind of shoes;
- Model 164 with a Ø190 mm holes can be used for woman and baby shoes;
- Model 165 with a Ø240 mm holes can be used for man shoes.
Technical details | |
---|---|
Dimensions: | cm 90 x 55 x 106 |
Net weight: | Kg 187 |
Air consumption: | 79 lt /cycle |
Daily production: | 1300 pairs |
: |
Sole assembly pneumatic at sink tube type
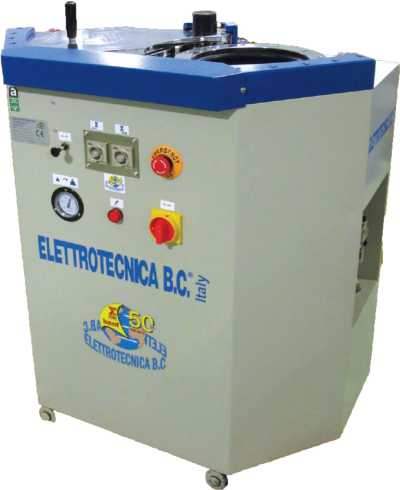
- Sole assembling pneumatic at sink tube type useful for all kind of shoes;
- Model 164 with a Ø190 mm holes can be used for woman and baby shoes;
- Model 165 with a Ø240 mm holes can be used for man shoes.
Technical details | |
---|---|
Dimensions: | Cm 90 x 55 x 106 |
Net weight: | Kg 187 |
Daily production: | 165 lt /cycle |
Daily production: | 1300 pairs |
: |
Machine at 2 stations programmable with touchscreen for humidifying the complete upper and reactivating toe-cap and counter before lasting operation. - patented -
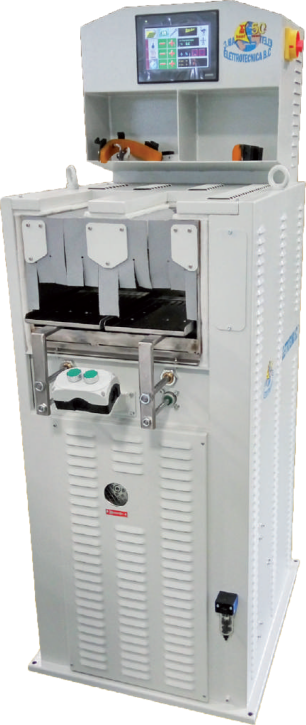
Operating cycle autoprogrammable for different materials. The heated dry steam, mixed with hot air, softs the upper without wetting it, allowing perfect shaping to be obtained during toe lasting operation.
- Steam quantity adjustable up to 6,5 m3/h
- Air temperature adjustable up to 200°c/392°f
- Working time programmable for each materials.
Technical details | |
---|---|
Dimensions: | cm 60 (24”) x 86 (34”) x 157 (62”) |
Net weight: | Kg 125 (275 LBS) |
Electric power: | Kw 7 |
Air consumption at 3 Bar: | 50 lt/min |
: |
Conveyor belt humidifier
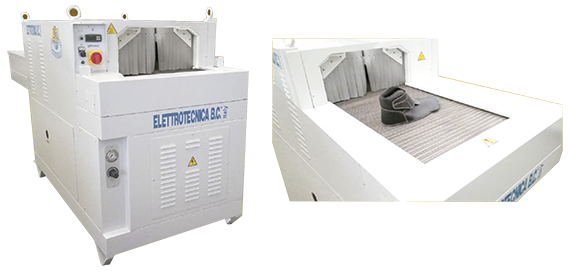
- This machine enables the operator of the lasting machine to avoid loading the humidifier permitiing a quantitative and qualitative increment in production of 25-30%
- the treatment of all the uppers is executed by use of steam at adjustable temperatures which notably reduces breakages during the lasting phase
- the mod. 269 w is equipped with a lateral conveyor for external transport of the moulds
- rink system compatible
Technical details | |
---|---|
Dimensions: | cm 95 (37”) x 224 (88”) x 115 (45”) |
Net weight: | Kg 200 (440 LBS) |
Electric power: | Kw 0,7 |
Air consumption: | 9,5 lt/pair |
: |
Programmed machine with opanka system - patented -
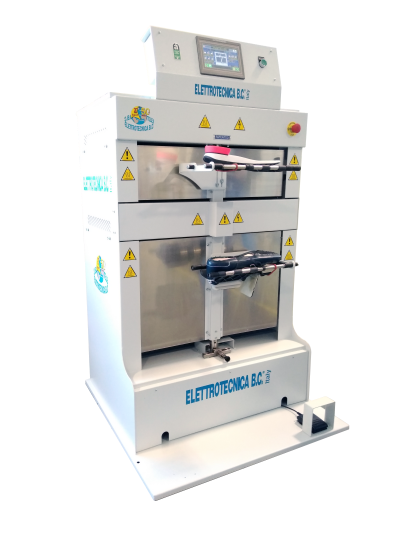
The 325NWPS/K allows to program the reactivation temperature in 12 different areas of the shoe and sole, giving the possibility
to achieve absolute temperature precision even in soles formed by of different material.
It is equipped with programmed devices also in the Opanka area of the shoe and sole.
The special shoe and sole support is designed for shoes / boots for children, men and women.
Technical details | |
---|---|
Daily production: | 1500 pairs in 8 hours |
Dimensions: | cm 91(36”) x 106,5(42”) x H159(62,60”) |
Net weight: | Kg. 95 (209 LBS) |
Absorbed Power: | Kw 16 |
Programmed conveyor belt cement drying machine with double reactivation and opanka system - patented -
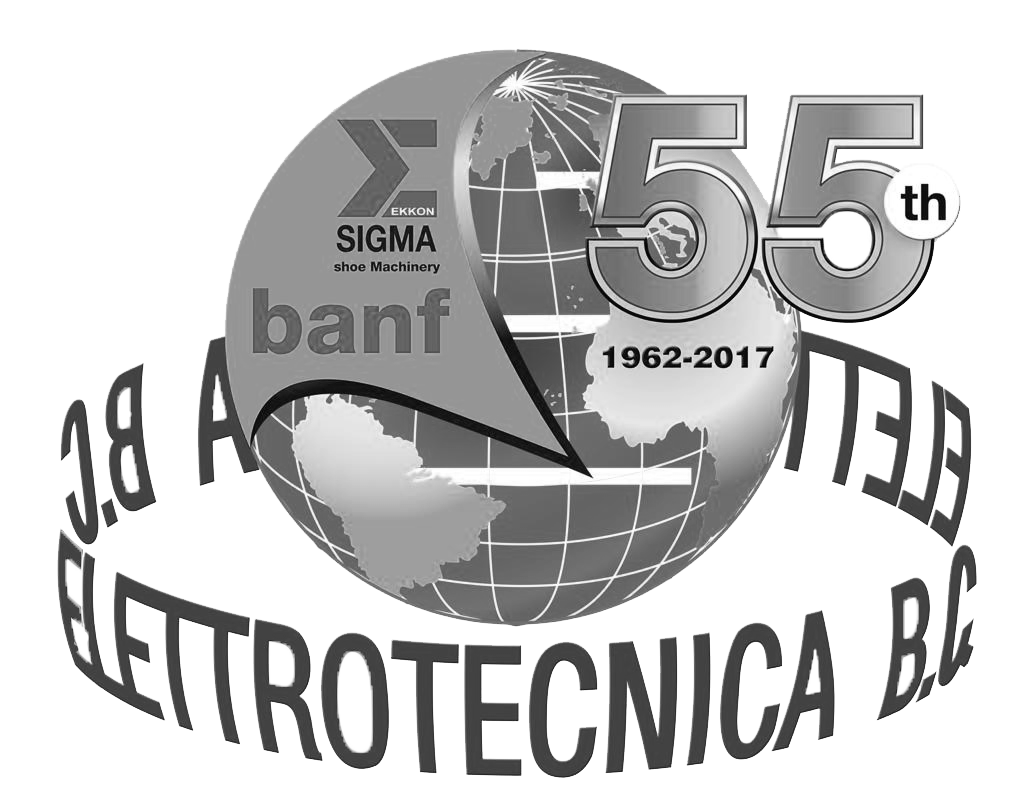
The cemented surfaces are dried and reactivated in 2~3 minutes, as apposed to 25~30 minutes in the past. In addition to substantial time saving this also reduces the number of last required. The specially designed conveyor enables soles and shoes/boots to travel in pairs thus easing assembly work by the operator. Moreover, the conveyor is adapted to any type of sole or shoe/boot. Rink system compatible.
Technical details | |
---|---|
Daily production: | 1500 pairs/hour |
Dimensions: | cm 105 (42”) x 350 (138”) x 168 (66”) |
Peso neto: | Kg. 580 (1279 LBS) |
Electric power: | 14 kW |
Conveyor belt cold conditioning unit
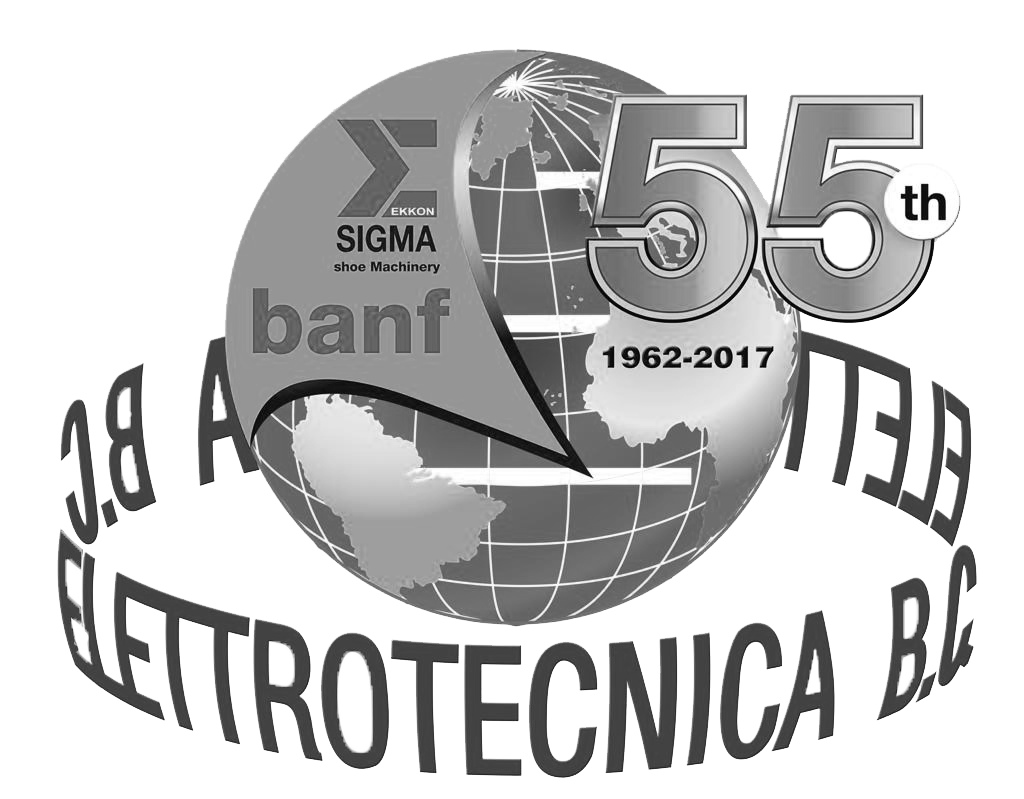
The conditioning unit permits rapid cooling, after the sole pressing, of all the footwear previously heat-treated, resolving problems deriving from very rapid work cycles - it accelerates stabilisation times of the footwear and the polymerisation times of the water based cements, guaranteeing perfect sealing - it rapidly cools and stabilises the soles and shoes produced by the P.U. Machines rink system compatible
Technical details | |
---|---|
Daily production: | 600 pairs in 8 hours |
Dimensions: | cm. 99(39,5”) x 106(41”) x 148(58”) |
Net weight: | Kg. 362 ( 798 LBS) |
Conveyor belt cold conditioning unit
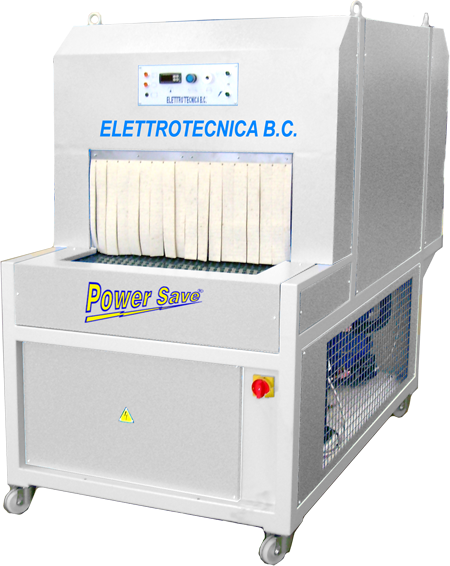
The programmed conditioning unit permits rapid cooling, of all the footwear previously Heat-treated, resolving problems deriving from rapid work cycles
- it accelerates stabilisation Times of the footwear and the polymerisation times of the water based cements, guaranteeing perfect Sealing
- - it rapidly cools and stabilises soles and shoes produced by the p.u.
- machines rink system compatible, - a touch screen colors permits to simplifying use for the Operator
- the new system is equipped With work cycles, in which is possible configure the machine to have load and unload from the Same part
- optimization extra ventilation programmed cycle, to get the maximum cold stabilization.
- the program is fitted with a function to calculate automaticly the permanent time of The footwear in base of the material type and the productivity that you want.
Technical details | |
---|---|
Daily production: | 600 pairs in 8 hours |
Dimensions: | cm 99(39,5”) x 106(41”) x 148(58”) |
Net weight: | Kg. 362 ( 798 LBS) |
Conveyor belt cold conditioning unit
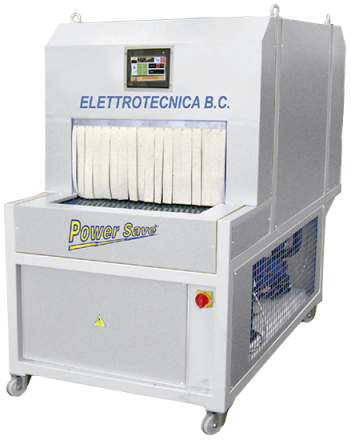
The conditioning unit permits rapid cooling, after the sole pressing, of all the footwear previously heat-treated, resolving problems deriving from very rapid work cycles
- it accelerates stabilisation times of the footwear and the polymerisation times of the water based cements, guaranteeing perfect sealing
- it rapidly cools and stabilises the soles and shoes produced by the p.u. Machines rink system compatible
Technical details | |
---|---|
Daily production: | 1000 pairs in 8 hours |
Dimensions: | cm 100(39,5”) x 180(71”) x 165(65”) |
Net weight: | Kg. 520 ( 1146 LBS) |
Absorbed Power: | 5,2 k |
Conveyor belt cold conditioning unit
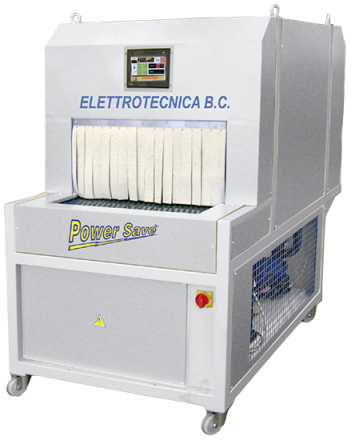
The programmed conditioning unit permits rapid cooling, of all the footwear previously Heat-treated, resolving problems deriving from rapid work cycles
- it accelerates stabilisation times of the footwear and the polymerisation times of the water based cements, guaranteeing perfect sealing
- it rapidly cools and stabilises soles and shoes produced by the p.u.
- machines rink system compatible,
- a touch screen colors permits to simplifying use for the operator.
- pre configured a series of materials which are ready for use.
- the new system is equipped with work cycles, in which is possible configure the machine to have load and unload from the same part.
- optimization extra ventilation programmed cycle, to get the maximum cold stabilization.
- the program is fitted with a function to calculate automaticly the permanent time of The footwear in base of the material type and the productivity that you want.
Technical details | |
---|---|
Daily production: | 1000 pairs in 8 hours |
Dimensions: | cm 100(39,5”) x 180(71”) x 165(65”) |
Net weight: | Kg. 520 ( 1146 LBS) |
Electric power: | 5,2 kW |
Conveyor belt cold conditioning unit
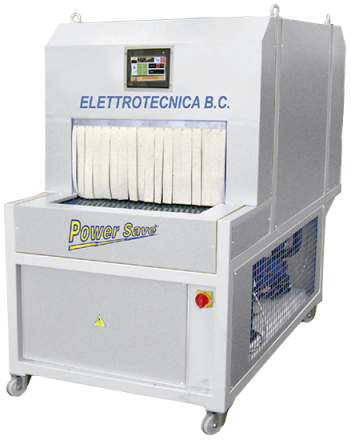
The conditioning unit permits rapid cooling, after the sole pressing, of all the footwear previously heat-treated, resolving problems deriving from very rapid work cycles
- it accelerates stabilisation times of the footwear and the polymerisation times of the water based cements, guaranteeing perfect sealing
- it rapidly cools and stabilises the soles and shoes produced by the p.u. Machines rink system compatible
Technical details | |
---|---|
Daily production: | 1600 pairs in 8 hours |
Dimensions: | cm 100(39,5”) x 225(89”) x 182(72”) |
Net weight: | Kg. 610 (1344 LBS) |
Absorbed Power: | 10,2 kW |
Conveyor belt cold conditioning unit
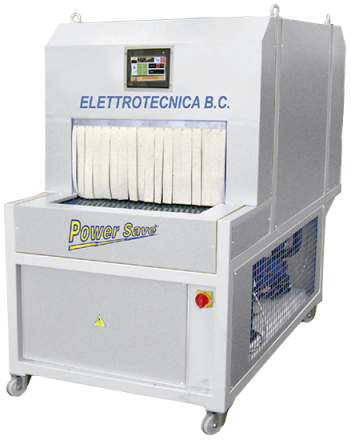
The conditioning unit permits rapid cooling, after the sole pressing, of all the footwear previously heat-treated, resolving problems deriving from very rapid work cycles
- it accelerates stabilisation times of the footwear and the polymerisation times of the water based cements, guaranteeing perfect sealing
- it rapidly cools and stabilises the soles and shoes produced by the p.u. Machines rink system compatible
Technical details | |
---|---|
Daily production: | 2000 pairs in 8 hours |
Dimensions: | cm 100(39,5”) x 390(154”) x 181(71,5”) |
Net weight: | Kg. 690 (1521 LBS) |
Electric power: | 18,6 kW |
High performance heat setter to ironing and conditioning shoes and boots lasted on last
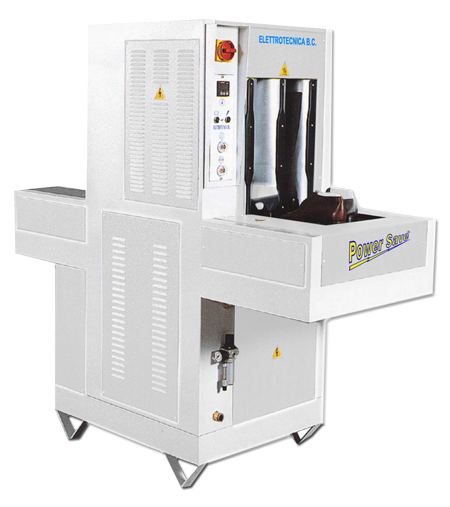
- Stainless steel ironlng chamber and conveyor belt
- Conveyor speed adjustable from 1' to 10"
- Steam quantity adjustabte up to 3000 cm3/h
- emperature on display adjustable up to 200 °C (392 'F)
- Rink system compatlble
Technical details | |
---|---|
Daily production: | 500 pairs in 8 hours |
Dimensions: | cm 65 (26”) x 165 (65”) x 150 (59”) |
Net weight: | Kg 220 (485 LBS) |
Electric power: | 6,2 kW |
High performance heat setter with autosetting thermal treatment, with final temperature reducer and inspiration hood - Patent Pending -
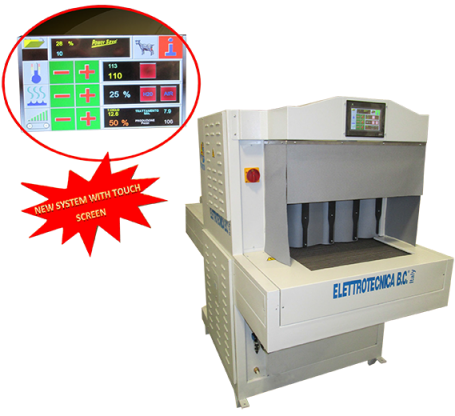
Machine to stabilize with hot steamed air all kind of footwear on last. System of automatic calculation rifle steam and temperature in relation of the output production. Visualization given of production and time of permanence of the footwear. Visualization percentage of humidity. Program preset up to you for the different material with possibility to set the heat treatment to article. Movement conveyor automatic depending to the request temperature. Fast reduction of the temperature in excess. System touch-screen video colours. System searches breakdowns
automatic with resolution of the problem. System of heat reduce on shoe to the exit of the thermal treatment.
- Times of the adjustable thermal treatments until 25”
- Temperature of the treatments adjustable until 200°C (392°F)
- Percentage of adjustable humidity until to one production of 3500cm3/h of steam
- Heat climate room, conveyor belt and steamer are in stainless steel material.
Technical details | |
---|---|
Daily production: | 2000 pairs in 8 hours |
Dimensions: | cm 100 (39”) x 260 (102”) x 157 (62”) |
Net weight: | Kg 370 (816 LBS) |
Gross weight with crate: | Kg. 460 (1015 LBS) |
: |
High performance heat setter with chill setter
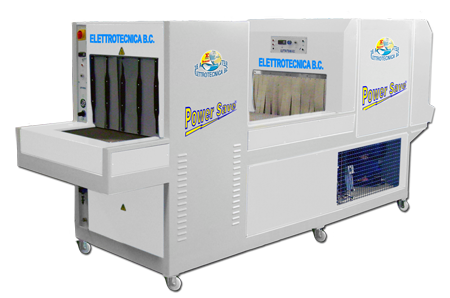
- Stainless steel ironing chamber and conveyor belt
- Conveyor speed adjustable
- Steam quantity adjustable up to 3000 cm3/h
- Temperature on display adjustable up to 200°C
- Anti-condensation double thermic insulant
- Automatic defrosting
- Adjustable temperature from 0°C to -20°C
Technical details | |
---|---|
Daily Production: | 150 pair for hour |
Dimensions: | cm 100(40”) x 405(160”) x 154(60”) |
Net Weight: | Kg. 900 (1984 LBS) |
Assorbed power: | Kw 10 |
High performance heat setter with chill setter
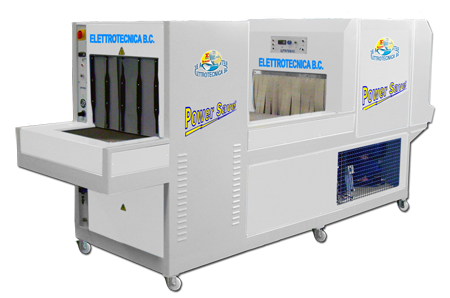
- Stainless steel ironing chamber and conveyor belt
- Conveyor speed adjustable
- Steam quantity adjustable up to 3000 cm3/h
- Temperature on display adjustable up to 200°C
- Anti-condensation double thermic insulant
- Automatic defrosting
- Adjustable temperature from 0°C to -20°C
Technical details | |
---|---|
Daily Production: | 200 pairs/hour |
Dimensions: | Cm 102(40”) x 450(177”) x 154(60”) |
Net Weight: | Kg. 1100 (2425 LBS) |
High performance heat setter with chill setter
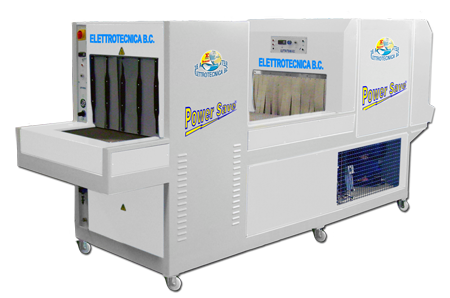
- Stainless steel ironing chamber and conveyor belt
- Conveyor speed adjustable
- Steam quantity adjustable up to 3000 cm3/h
- Temperature on display adjustable up to 200°C
- Anti-condensation double thermic insulant
- Automatic defrosting
- Adjustable temperature from 0°C to -20°C
Technical details | |
---|---|
Daily Production: | 275 pairs/hour |
Dimensions: | Cm 105(41”) x 690(271”) x 172(67”) |
Net Weight: | Kg. 1190 (2624 LBS) |
Assorbed power: | Kw 29 |
Pneumatic assembling for soles complete at 1 station
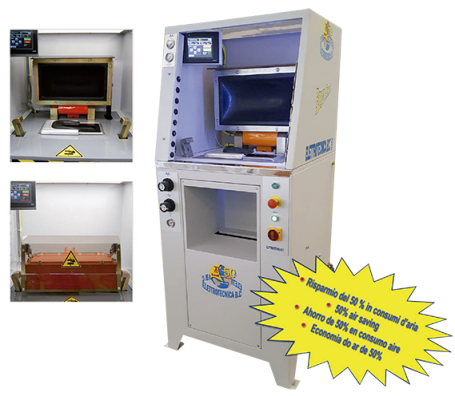
Pneumatic assembling machine programmed for soles with blowing up bell
• Double inner chamber, one first pressure, one second pressure
• Adapted to whichever type shoe and boot
• Equipped of photoelectric cells for starting the automatic cycle and, for the emergency of the operator
•The shoe support is adjustable in vertical and horizontal
• New cycle of release that allows to speed the cycles
and to diminish the air consumption and the usury of rubbers
• It has a air storage cell and a pneumatic system with double capacity of vacuum.
Adjustable times of first and second press individually until 30" • Adjustable pressures first and second press individually
Technical details | |
---|---|
Dimensions: | cm 90 (35,4”) x 65 (25,6”) x 170 (67”) |
Net weight: | Kg 250 (551LBS) |
Last support for manual assembly of shoes/boots.
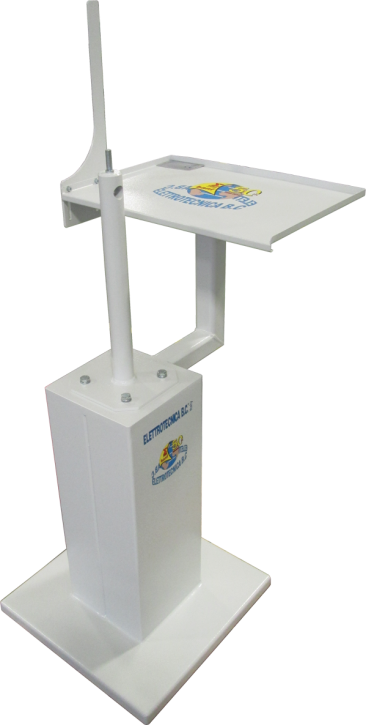
Technical details | |
---|---|
Dimensions: | cm 52 (20”) x 73 (29”) x 105 (41”) |
Net weight: | Kg 53 (117 LBS) |
Table for gluing with aspirator and led lights.
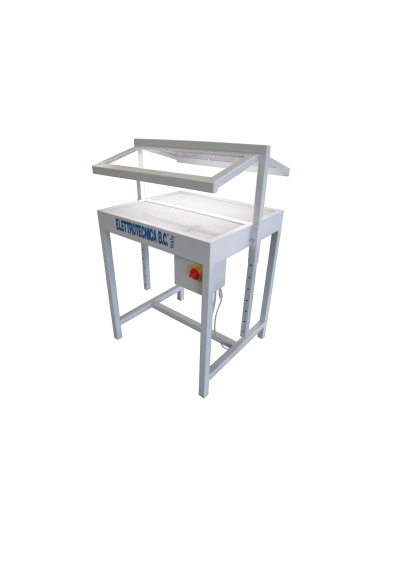
Table with illuminated worktop and height-adjustable safety screen that can be adapted to any type of work.
Working area cm 73 (29”) x 63 (25”)
Technical details | |
---|---|
Dimensions: | cm 88 (35”) x 70 (27”) x 127 (50”) |
Net weight: | Kg 56 (123 LBS) |
Electric power: | Kw 0,8 |
PHOTO GALLERY
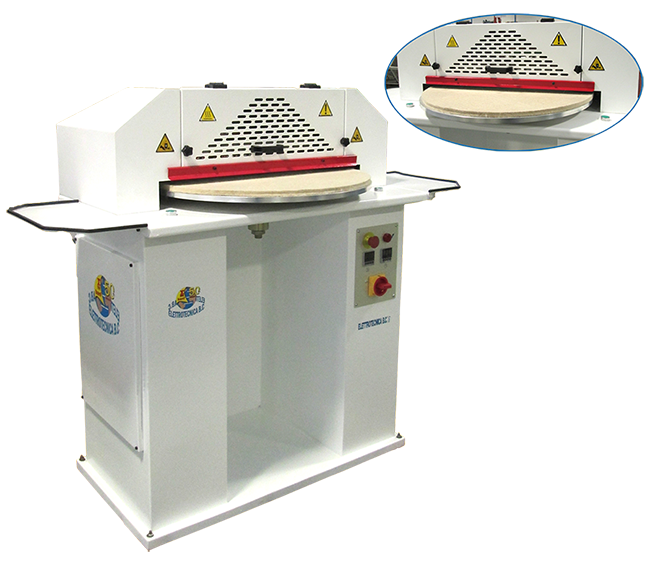
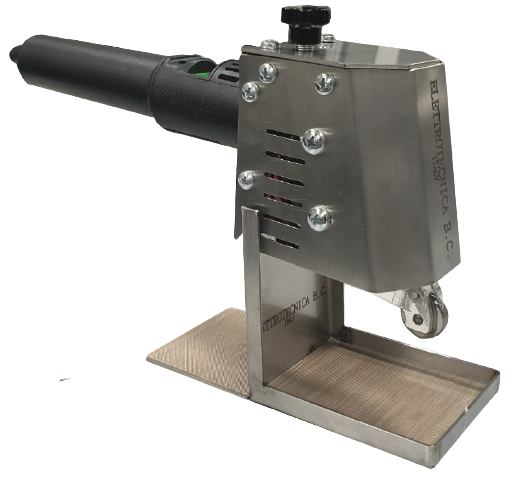

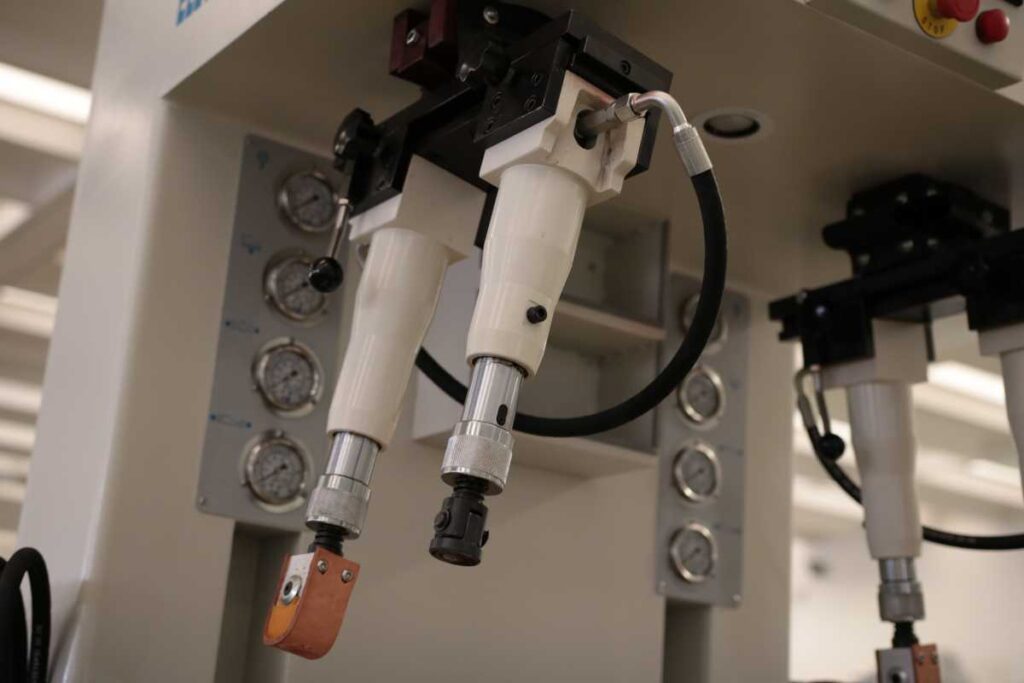
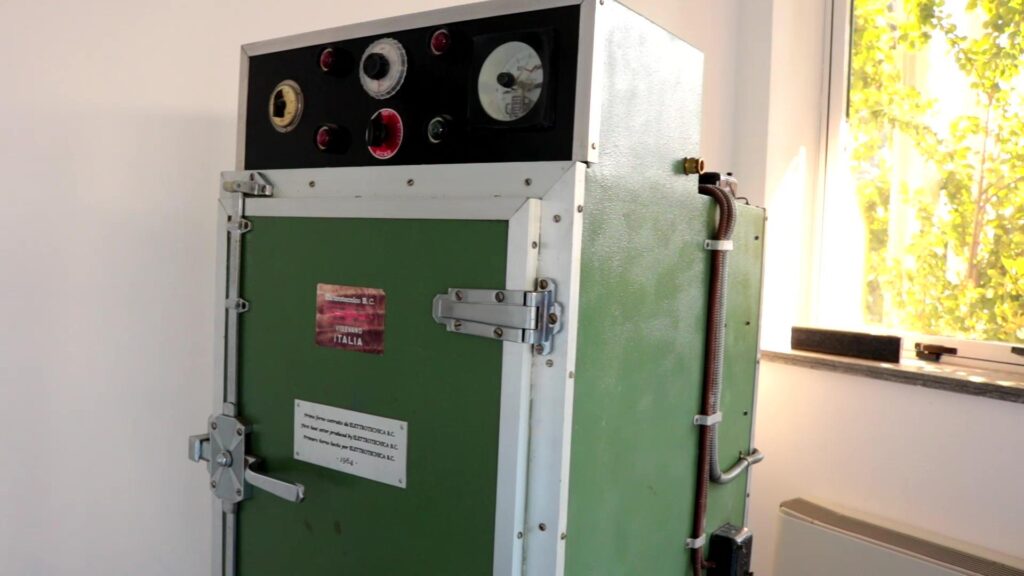
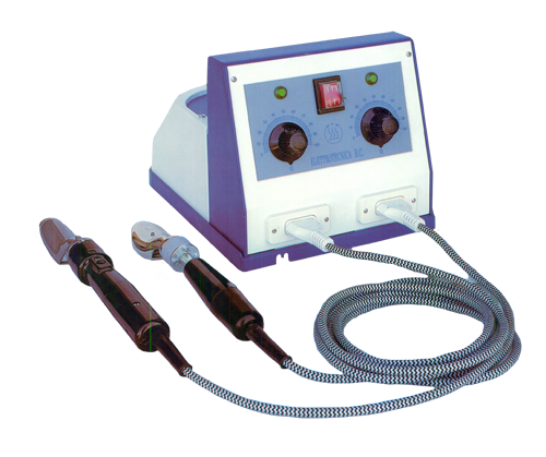
Contact us for more informations!
Fill out this form to request informations about our products.